The Gift of South Dakota
Subscriptions to South Dakota Magazine make great gifts!
Subscribe today — 1 year (6 issues) is just $29!
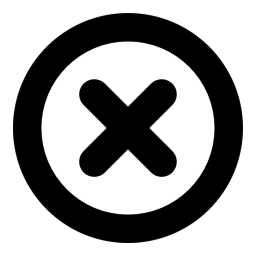
Forging Youth
![]() |
Faculty, students and working blacksmiths gather around forges at South Dakota Mines in Rapid City. |
Methinks if the Knights of the Round Table sailed to America today, they’d soon be drawn to Rapid City, where young bladesmiths are gaining a reputation on the campus of South Dakota of Mines.
When classes end on Friday afternoons, the youth can be found at an old-style blacksmith shop on the edge of campus, hammering red-hot metal into knives, swords and less-practical items like jewelry, animal likenesses, ornate scrollwork and roses with a burnt aroma. They chatter and share insights as gleaming coals heat the steel to more than a thousand degrees. The pungent smell of melting metal and the clanging of hammers add to an already-unusual campus atmosphere.
Why is an ancient skill developed during the Iron Age such a rage 3,000 years later at a university touted for modern science and technology? “Bladesmithing is a microcosm of metallurgy and the engineering processes associated with modern manufacturing,” explains Dr. Jon Kellar, a veteran Mines professor partly responsible for students walking around campus today with knives and swords.
Fourteen years ago, Kellar was watching a public television show titled Secrets of the Samurai Sword when he noticed that his young son was captivated by the history and science. It dawned on him that youth who are interested in medieval and Renaissance culture might also be intrigued by metallurgical engineering. Soon there was a Blacksmithing Club on campus, and all the school’s faculty embraced the idea of welcoming and recruiting teens who like fire and danger.
School of Mines professors also became involved in blacksmithing organizations, and they urged The Minerals, Metals and Materials Society (TMS) to create an international bladesmithing contest for engineering students.
Before long, students were making swords at Mines, some using iron ore from the Black Hills. Just as Kellar hoped, the school’s awakening to blacksmithing has attracted students.
“I am more of an artistic person,” says Tony Romero, a third-year engineering student, “but the more you get into it the more you realize the connection between art and science.”
Romero says his interest in the artistry of swords and knives has been life changing. “The gateway drug to blacksmithing is blade smithing,” he says.
The blending of art and science is also forging a bond between high school students, South Dakota blacksmiths and major Midwestern manufacturers.
![]() |
Isaac Hammer (left) and Tony Romero typify Mines students who appreciate hands-on learning, especially when fire and metal are involved. |
Companies like John Deere and Nucor Steel, who rely on metallurgical engineers, saw the connection and support the school’s efforts. “If you go to their facilities, you soon see that it’s just blacksmithing on a much higher scale with much bigger furnaces,” says Kellar. Consequently, playing with tongs and hammers in Rapid City has led to careers for students who might never have imagined themselves engineers.
Bladesmithing brought worldwide attention to the School of Mines when a team of students won the 2017 international collegiate blacksmithing competition by forging a 34-inch blade fashioned after a 10th century sword found in a burial mound in Norway. The spine of the intricate blade was made from Black Hills iron ore.
The winning sword — exquisitely etched with artistic spirals and swirls — is now exhibited along with the trophy plaque behind glass in the hallway of the Metallurgy Building. It is the school’s holy grail for students who hope to repeat the accomplishment.
The story of the sword is now campus legend. Isaac Hammer, a junior student who leads the Blacksmithing Club, knows the names of the seven students on the 2017 team and he’s hoping he and his friends can add to the trophy case. The biannual competition was cancelled last year due to COVID-19, but Mines students are practicing to defend the title.
The Blacksmithing Club has also taken on the task of helping younger people; they’ve assisted Boy Scouts with merit badge projects related to metallurgy, and they host an annual summer workshop for high school students called “The Science of Swords.”
Conversely, the collegians receive support from South Dakota’s blacksmiths — especially Jack Parks, who runs Fire Steel Forge at nearby Piedmont. Parks, 72, remembers what it’s like to get started. “I was a young guy who liked doing stuff with my hands and I wanted to work with metal, but all I had was a claw hammer, a hacksaw and an electrical drill and I couldn’t get anywhere. Then I started playing around with fire and heating metal, and I saw how easily it would bend.”
Parks wrangled an apprenticeship with Keystone blacksmith Harvey Brunner, a cowboy who pioneered metal art in South Dakota. Parks practiced it as a hobby for 10 years before becoming a full-time artisan who has gained a reputation for creating architectural accents. He crafted railings for the State Game Lodge in Custer State Park and recently restored historic fences at Mount Moriah Cemetery in Deadwood.
Parks sees his younger self in the students at the School of Mines. “Blacksmithing has something that has always attracted certain people because it has all the elements that kids like,” he laughs. “Fire, smoke, noise and danger.”
![]() |
Tyler Reinarts says he likes the history behind bladesmithing. |
The Piedmont blacksmith credits the Mines faculty for recognizing an unconventional learning opportunity. “They’ve got some pretty sophisticated scientists and engineers there, but the blacksmithing part was lacking and they knew it could be an important part of the program.
“You can lay on your back and think about stuff and it really doesn’t teach you as much as if you do something with your fingers, even if you make mistakes,” Parks says. “There’s a connection between the brain and the fingers. The fingers help the brain learn and I think sometimes that is getting lost.”
Other hands-on blacksmiths who help the youth include Nick Hix, Woody Hanson and Erich Orris of Rapid City, Steve Grosvenor of Beresford, and Clark Martinek, an iron artist in Mitchell.
K.J. Groven, a Sturgis woodworker and blacksmith, is another key volunteer. Groven was born in Skien, Norway and worked on a family farm until 1999 when he emigrated to study mechanical engineering at Rapid City. He’s made a career in South Dakota of creating Scandinavian style buildings, furniture and tools.
Dr. Mike West, a colleague of Kellar, says some of the school’s bladesmithing culture should also be credited to Kevin Gray, who visited campus as a high school student with his handmade 8-inch knife in a backpack. Gray wasn’t carrying the blade for self-defense; he just wanted to show it to someone who might share his interests. Gray did enroll at the School of Mines, but due to financial hardships he left before graduation to earn money in the coal fields of Wyoming.
Believing in Gray’s ability and skills, the faculty developed an independent study program for him that included a special project in the blacksmith shop. He exceeded their expectations, documenting the properties of the steel that he hammered. He graduated, landed a position with Nucor Steel in Norfolk, Neb., and now returns to campus to help younger bladesmiths.
Such is the community growing around metallurgy labs, classrooms and that old-time blacksmith shop below Smelter Hill. Legend says King Arthur created the concept of the Round Table because he wanted his swordsmen to have an equal place. A man like that would love the comradery being forged around steel and fire in the black forest of South Dakota.
Editor’s Note: This story is revised from the July/August 2021 issue of South Dakota Magazine. To order a copy or to subscribe, call (800) 456-5117.
Comments